Beim Airbus-Testflug im Cockpit
„Wir können mit einer großen Wahrscheinlichkeit davon ausgehen, dass das Flugzeug fliegen wird“ – ein Satz, den normalerweise bei Airbus niemanden in Unruhe versetzt. Es sei denn, er kommt aus dem Mund eines Testpiloten, der gerade einem Journalisten erklärt, warum in den nächsten 90 Minuten einige Manöver weit jenseits des normalen Flugprofils eines Passagierfluges anstehen. Nicht irgendwo. In 10,6 Kilometern Höhe in einem nagelneuen Airbus, der demnächst ausgeliefert werden soll – wenn die entsprechenden Phasen beim Testflug erfolgreich verlaufen. „Wir fliegen absichtlich in den roten Bereich“, sagt Pilot Peter Koch. Was für den DEICHLUST-Reporter nicht ermutigend klingt.
Es ist einer der trüben Tage an der Elbe. Normalerweise wären wir bereits in der Luft, aber der Nebel über dem Airbuswerk in Finkenwerder lässt keine Flugbewegung zu. Doch der Wetterbericht verspricht Besserung, was für die Piloten eine gute Nachricht ist.
Dass ein Journalist überhaupt beim Testflug mit im Cockpit sitzen darf, ist eher ungewöhnlich, ich weiß es zu schätzen. Ich glaube, in sicheren Händen zu sein, denn mit dem Piloten Peter Koch hatte ich bereits ein anspruchsvolles Manöver erleben dürfen. Einen Startabbruch auf der Startbahn in Finkenwerder – ein Airbus mit Vollbremsung bei Tempo 180. „Leg das Handy weg, es wird dir sonst aus der Hand geschleudert“, hatte Peter Koch gewarnt, nach nicht einmal 15 Sekunden war das Manöver beendet, das zu einem Testflugprogramm gehört, das jeder Jet vor der Auslieferung absolvieren muss.
Detailliert ist von den Zulassungsbehörden vorgeschrieben, was bei einem Startabbruch getestet werden muss. Im Flieger werden umfangreiche Daten aufgezeichnet und analysiert, in der Kabine werden die Verkleidungen und Kommunikationssysteme überprüft. Wenn alles in Ordnung ist, darf der Airbus erstmals starten und diesmal auch abheben. Nach dem Erstflug folgt ein Kundenflug mit den Piloten der Airline an Bord. „Da geht es dann darum, gemeinsam mit dem Kunden nochmal einige Manöver zu fliegen und vor allem auch die Kabine nochmal durchzuprüfen“, sagt Peter Koch. Danach wird der Flieger ausgeliefert, wenn alles funktioniert hat. „In den allermeisten Fällen sind die Flieger in Ordnung, am Rest gibt es meist nur kosmetische Operationen“, sagt Testingenieur Thomas Heidemann. Aber: Es gibt durchaus auch Fälle, wo nachgearbeitet wird. So lassen sich zum Beispiel Geräusche an den Türen nur feststellen, wenn das Flugzeug mit hohem Tempo durch die Luft fliegt. Das lässt sich nicht am Boden testen. Entsprechend wird dann nach der Rückkehr vom Kundenflug nochmal nachjustiert.
Wir sitzen in einem unspektakulären Besprechungsraum in der Flugerprobungsabteilung bei Airbus in Finkenwerder. 45 Ingenieure und Testpiloten absolvieren im Durchschnitt ein bis zwei Testflüge am Tag, am Standort ausschließlich mit den Fliegern aus dem erfolgreichen A320-Programm.
Geflogen wird im normalen Luftraum der zivilen Luftfahrt, Fluglotsen räumen den Weg für die Testflieger frei. Heute hat eine Frau aus der Kontrollzentrale in Karlsruhe das Kommando, sie legt die Route so, dass der Testflug vom Linienflugverkehr nicht gestört wird. Noch wissen wir nicht, wohin wie fliegen werden. Airbus nutzt für die Produktionsflüge die Lufträume über Nord- und Ostsee.
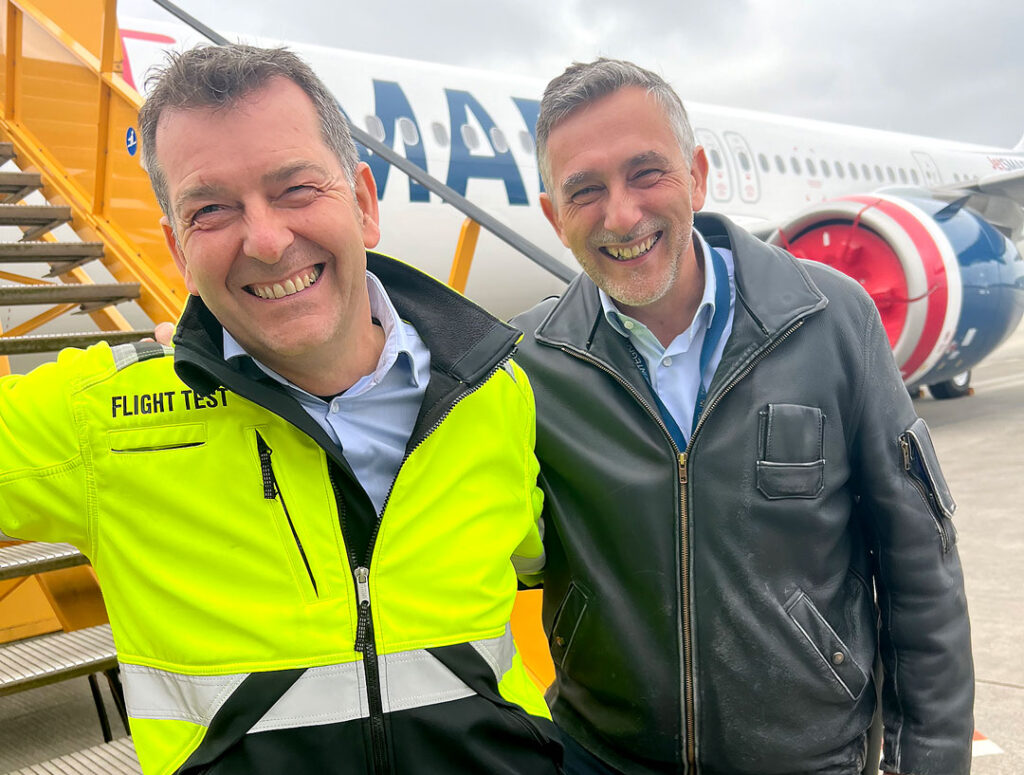
„Wir fliegen ständig, aber kommen nie an“,
sagt Thomas Heidemann über den Job. Gestartet wird nämlich immer in Finkenwerder und gelandet – auch immer in Finkenwerder.
Der Scherz ist schnell verflogen, denn Peter Koch erklärt die dynamischen Phasen des Flugs: Ein 30-Grad Steigflug mit anschließendem steilen Sinkflug. Der Jet wird in extreme Schräglagen bis zu 67 Grad versetzt, beschleunigt innerhalb von 15 Sekunden um 300 km/h, um später bei circa 100 Knoten an die Grenze zu einem Strömungsabriss zu gehen. Zum Vergleich – bei einem normalen Passagierflug beträgt der Winkel beim Steigflug rund 15 Grad und beim Kurvenflug neigt sich das Flugzeug nur um wenige Grad. Doch die maximale Schräglage ist auch ein Sicherheitsfaktor – vielleicht benötigt die Crew diese später einmal für ein Ausweichmanöver im Notfall.
„Danach gehen wir in Richtung Mount Everest“, kündigt Thomas Heidemann an, was aber nicht geografisch zu verstehen ist. Der Luftdruck im Flieger wird bewusst abgelassen und entsprechend dünn. Der Pilot sagt fast väterlich: „Wenn die Fingerkuppen zu sehr kribbeln, sag Bescheid, dann brechen wir ab.“ Normalerweise herrscht in einem Passagierflugzeug während der Reise ein Druck wie in 8.000 Fuß oder 2.700 Meter, also etwa wie auf der Zugspitze. Wird die Luft noch dünner, schlagen diverse Warnsysteme an und im weiteren Verlauf würden die Sauerstoffmasken auslösen.
Peter Koch (55 Jahre) ist einer der erfahrensten Testpiloten bei Airbus. Der gebürtige Cuxhavener hat Luft- und Raumfahrtechnik studiert, Abschluss Diplomingenieur, danach Ausbildung zum Testpiloten beim Militär in Frankreich.
„Ich kann im Prinzip alles fliegen“, sagt der in Buxtehude wohnende Pilot, der rund 4.000 Testflüge auf über 40 Flugzeugtypen absolviert hat.
Peter Koch
Thomas Heidemann hat Elektrotechnik studiert, danach die Ausbildung zum Verkehrspiloten abgeschlossen, seit 22 Jahren ist er Testpilot, aber auch Flight-Test-Ingenieur, in dieser Funktion sitzt er jetzt mit im Cockpit. Als Co-Pilot ist der Franzose Manuel Lyne an Bord und in der Kabine prüft Kai Nordbruch die Systeme.
Um 09.34 Uhr werden wir mit dem Crew-Shuttle zum A321-Flieger gebracht. Take Off soll um 10 Uhr sein. Thomas Heidemann hat zuvor die Formalitäten erledigt, die Systeme sind von Technikern geprüft, im Cockpit werden jetzt die Flugvorbereitungen abgewickelt – letztlich wie bei jedem Linienflug. Bei Flugzeugen, die bereits zugelassen und in der Serienfertigung sind, gibt es den so genannten Production Flight Test. Das Flugzeug wird bei dem Flug außerhalb der Komfortzone bewegt – vor allem für Passagiere – aber es wird nicht an die Grenzen gebracht, wie bei einem Entwicklungstestflug (Development Flight Test). Für die erstmalige Zulassung eines Flugzeuges, das später in Serie gehen wird, wird in mehr als 2.000 Flugstunden ein Katalog abgearbeitet, in dem auch Tests bis an die Grenzen des Fliegers vorgesehen sind.
Bei unserem heutigen Production Flight Test geht es vor allem darum, zu sehen, ob die diversen Warnsysteme wie vorgesehen auslösen und die Notsysteme funktionieren. Für Erklärungen hat die Crew jetzt keine Zeit mehr. Die Fluglotsen aus dem Tower in Finkenwerder haben die Starterlaubnis erteilt und auch die Testcontrollerin in der Radarleitstelle Karlsruhe ist an ihrem Arbeitsplatz bereit.
10.01 Uhr, der A321 ist in der Luft, die Elbe nach nur wenigen Sekunden außer Sicht, die Wolkendecke hängt tief. Nach dreißig Sekunden blendet uns die Sonne, der Flieger ist im Steigflug, 10.000 Fuß sind erreicht. Die ersten System-Checks beginnen, wir steigen weiter, denn der Härtetest sind die 39.000 Fuß für unseren Probelauf mit den Systemen zur Regulierung des Kabinendrucks. Die Fingerkuppen kribbeln da oben dann tatsächlich, aber die Crew macht einen munteren Eindruck. Also schweige ich.
Die anschließende Steilkurve zum Sinkflug würde im Linienverkehr vermutlich einige Stoßgebete hervorrufen, auch Minimal-Geschwindigkeit wird nicht zum Problem. Peter Koch grinst nur, bei allen Manövern strahlt er Sicherheit und Gelassenheit gleichzeitig aus. Gut eine Stunde sind wir in Reiseflughöhe. Wir sind mittlerweile irgendwo von der Ostsee wieder zurück über der Nordsee und im Landeanflug. Ziel Fuhlsbüttel, höre ich über Funk. Fuhlsbüttel? Also doch irgendwas nicht in Ordnung?
„Hatten wir vergessen zu erwähnen“, sagt Thomas Heidemann, der meinen leicht erstaunten Blick richtig deutet. „Wir gehen in Fuhlsbüttel runter bis zum Minimum und starten dann durch“, erklärt er. Damit wird das automatische Landesystem getestet, welches bei Nebel das Flugzeug bis zur Landebahn führt. „Damit du alles erlebt hast.“ Startabbruch, Landeabbruch und den Ausfall zahlreicher elektronischer Systeme. Wie bitte? „Das kommt noch, aber keine Panik, wir testen nur die Ram Air Turbine, eine kleine ausfahrbare Turbine, die zum Einsatz kommt, wenn an Bord die gesamte Elektrik ausgefallen ist. Es ist ein kleiner ausklappbarer Propeller, der im Prinzip wie ein Fahrrad-Dynamo funktioniert – durch den Luftstrom wird Strom und Hydraulikdruck erzeugt und damit lässt sich das Flugzeug noch steuern. „Außerdem segelt so ein Flugzeug immer“, wirft Peter Koch ein.
Was spektakulär am 15. Januar 2009 in New York bewiesen wurde, als nach dem Start gleich beide Triebwerke eines Airbus A320 durch Vogelschlag ausgefallen waren und es den Piloten gelang, den Flieger aus dem Steigflug in einen Gleitflug zu bringen, mit anschließender Landung im Hudson River. Alle 155 Menschen an Bord überlebten. „Eine Meisterleistung“, kommentiert Peter Koch. Nicht nur die Landung hat ihn beeindruckt: „Diese Entscheidung zu treffen – davor ziehe ich meinen Hut.“
11.34 Uhr. Es ist ein Blindflug bei dichtem Nebel auf die Landebahn 23 – Richtung Süd-West am Helmut Schmidt Airport. Wir sinken und sehen nichts. Koch hat die linke Hand am seitlichen Steuerhebel und die rechte am Schub. 100, 80, 70, 60… „Go around“, und schon steigen wir wieder zum kurzen Heimflug über die Elbe. Das flaue Gefühl im Magen war zu ertragen. Zehn Minuten später landen wir in Finkenwerder.
11.54 Uhr, Ende eines Dienstfluges. Dem neuen Airbus wird die Flugtauglichkeit bescheinigt. „Wir unterschreiben das Zertifikat und die Behörde stellt die Zulassung aus“, sagt Heidemann. Nach dem Abnahmeflug mit den Piloten der Airline ist dieser Flieger für die Testpiloten Geschichte. Wie die zuvor 10.821 ausgelieferten Flugzeuge auch.
„Wie fast immer ohne besondere Vorkommnisse“, bilanziert Thomas Heidemann,
der in 23 Jahren nach eigenen Angaben „keinen schlimmen Vorfall in der Luft“ erlebt hat. Die Heimfahrt mit dem Auto sei weitaus risikoreicher. Sagt er mit einem Grinsen im Gesicht.
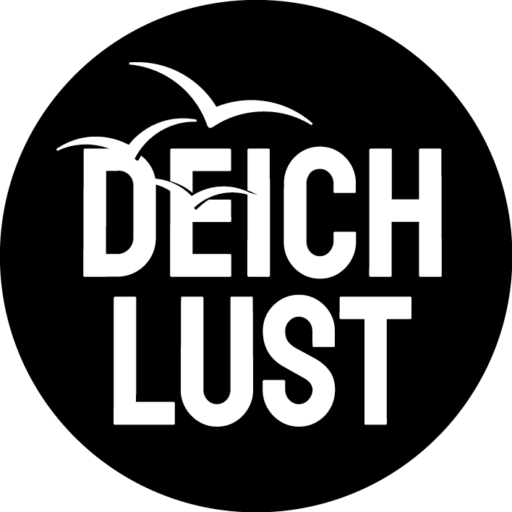
Text & Fotos: Wolfgang Stephan